Over the years, JP-TECH has developed an internal protocol that allows it to obtain excellent results in the design and construction of its machinery as well as in the testing and commissioning phase.
- Everything starts from the study and analysis phase of the problems to be solved
- Then we move on to the design phase in which JP-TECH interfaces with its technicians and collaborators for the development of the project.
- Now is the time for construction, JP-TECH in its production site builds most of the components internally and takes care of the assembly of the entire machine / line.
- After the realization of the machinery / line, JP-TECH in its headquarters carries out the testing with the reference material (supplied by the customer).
- Once scrupulous verification and testing tests have been carried out, JP-TECH also takes care of the installation at the customer's premises.
- Finally, a further test is performed at the customer's premises and at the same time all the necessary documentation is delivered to the company to define the machinery as "READY AND USABLE".
PROJECT
JP-LCS 028
The newly built calender is specifically a 3-rolls calender with a "Y" configuration, optioned to guarantee variable speed and friction, all to guarantee the customer the ability to work different products.
In addition to the primary machinery, we have also supplied accessory machines, completing a line that can process all the products of the client company.
In particular, the line is equipped with:
- Weaving system with reel change "on the run"
- Machine for cutting, scrap recovery and material embossing
- Machine for heating the product and, if necessary, applying special material
- Product cooling machine
- Automatic winder
The line is fully equipped for data control and reading as per the Industry 4.0 Plan.
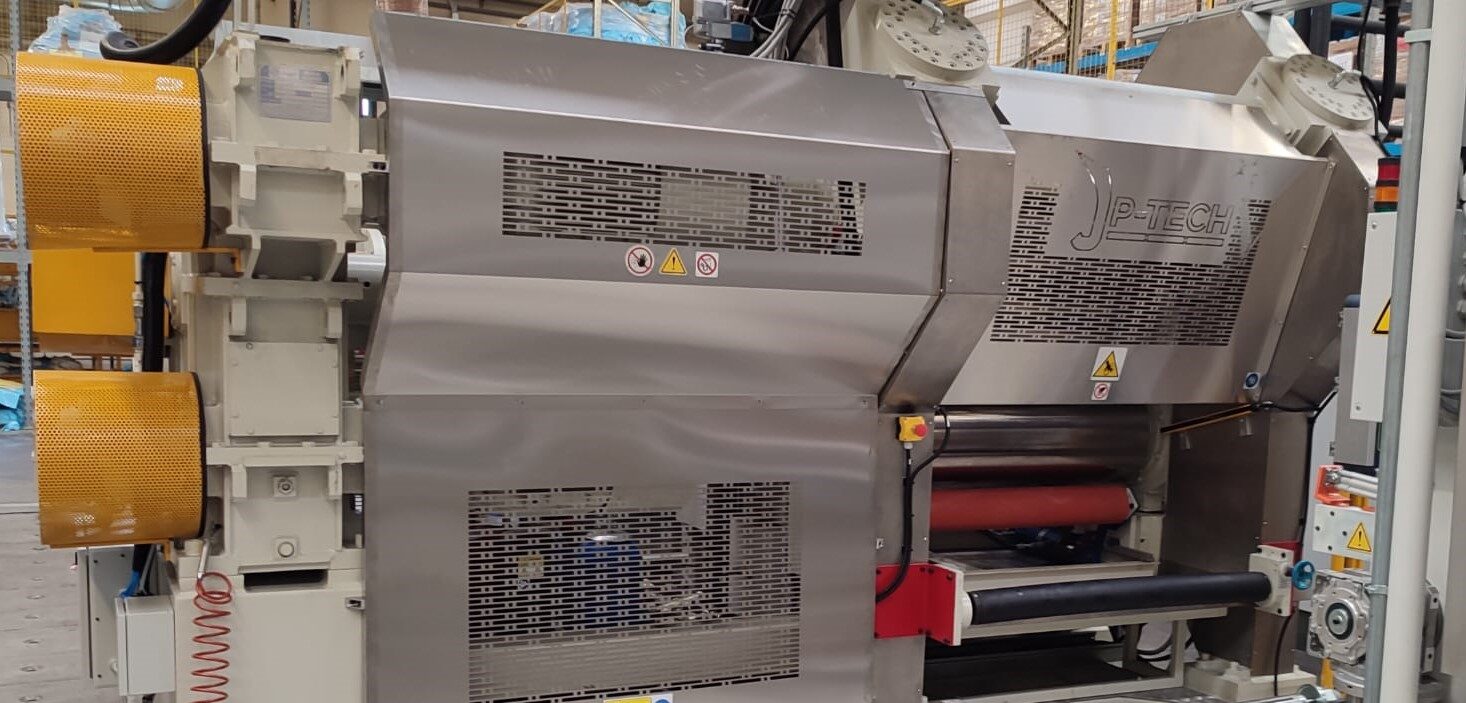
The machine has been completely overhauled as new, indeed we have done much more.
The MOOG Electrohydrostatic systems have been installed on the machine for the first time in the world, which will allow the machine to move the mobile cylinder with a few liters of oil (the previous systems used about 200), as well as almost non-existent energy consumption.
JP-TECH has been offering green machines on the market for years with the latest technologies for the sector applied. Attention to energy and oil consumption has always been a strong point of JP-TECH.
A heartfelt thanks goes to our customer Vibram Group for having accepted the challenge of assembling these innovative systems. Vibram has been focusing on sustainability and a Totally Green of production for years, thanks to a staff attentive to the technological needs of the market and always ready to adopt the most innovative solutions.
A special thanks goes to our Partners who have worked with us to achieve this goal Moog Inc. ROGAL S.R.L. Multi Data s.r.l. Maier Italia UTP TP Pneumatic Technologies Sella Srl
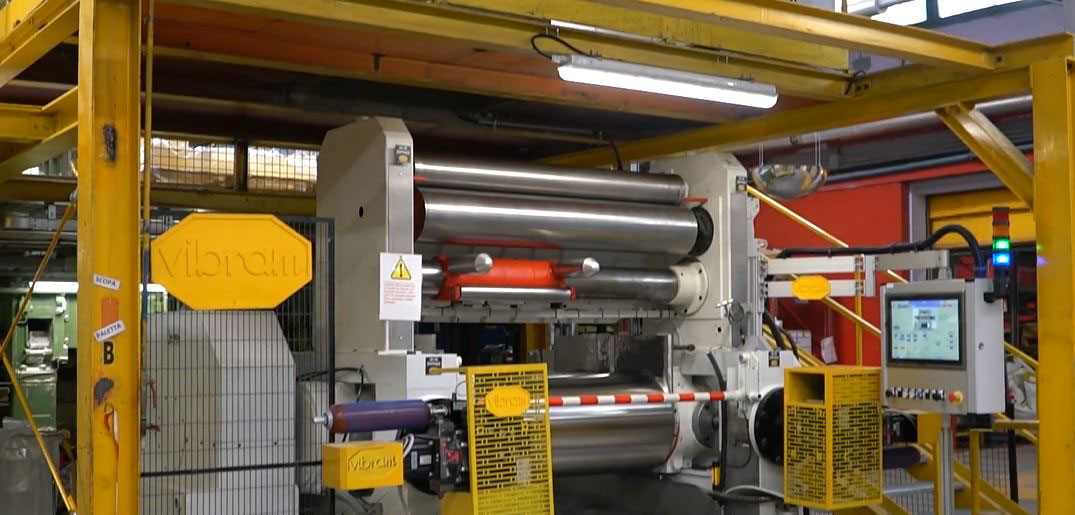
JP-MJR3
The mixing mill for rubber JP-MJR3 is a machine that, in addition to respecting all the particularities and characteristics of the previous models born in JP-TECH, “has been enriched with” new features.
Mounted on it are the new EAS systems born in collaboration with Moog which have now been improved with the part we patented which makes them even more efficient and sustainable.
In addition to the new patented systems we have implemented our software with the automatic management of all the mixing phases.
The software has also been improved in the control of energy saving and in the control of the components present on the machine.
The software is able to alert the operator and maintenance technicians to carry out checks on lubrication fluids, greasing the guides and checking the wear of the braking system, in addition to many other signals.
Another fundamental part is the constant monitoring of the safety systems.
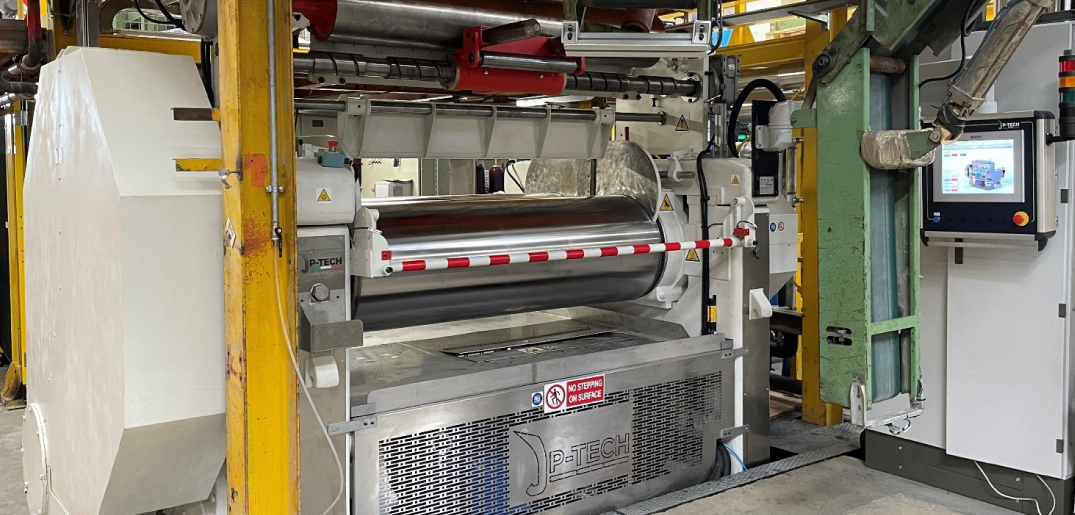
ELSA JP-AG002 DG
Compact size and with the possibility of arranging the system with a different layout compared to the one presented in the film.
The line consists of several primary blocks that are actually four different machines that can also be used as autonomous machines.
The automatic warehouse of the product to be processed is thermostated and can keep the product at temperature both in heating and cooling.
The filter press, which can work automatically, providing precise information on the state of the product production process.
Trommel complete with cutting and framing unit with integrated system, cooling of the finished product
The system allows you to work in: manual, semi automatic, automatic with operator panel, voice module and data acquisition system.
A series of data and information is available for both the operator and the quality control laboratory.
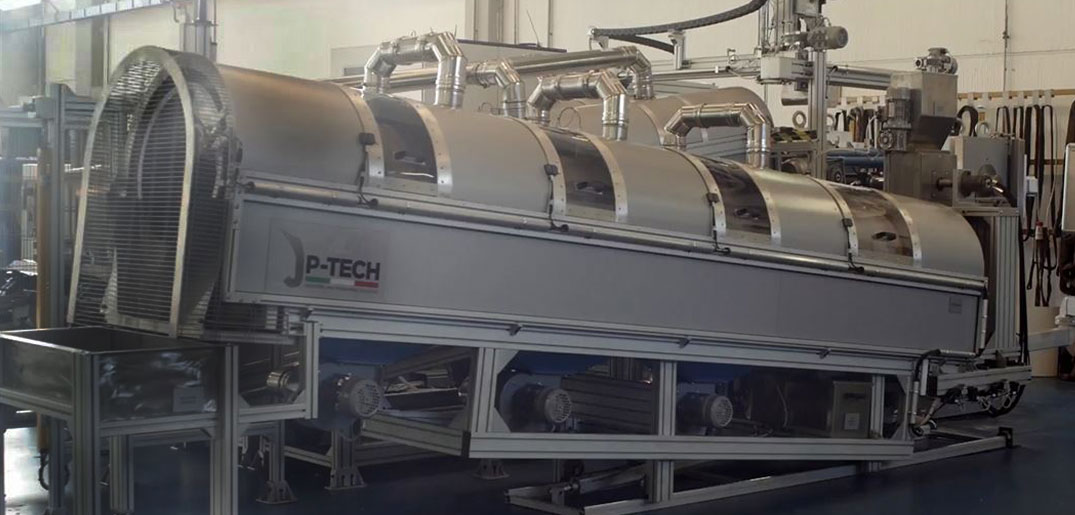
Lisa is able to handle all operations completely automatically.
The parameters are entered by means of a Touch-screen.
All the parts that make up the machine and the related data are displayed
on the Touch-screen.
The work phases managed by LISA are:
1. rubber coil unwinding
2. coupling with the double-sided
3. detachment of the protection of the double-sided
4. recovery of the double-sided film
5. polyethylene protection application
6. winding-cut-half cut
7. Automatic tape speed management
8. Automatic synchronizing reel speeds
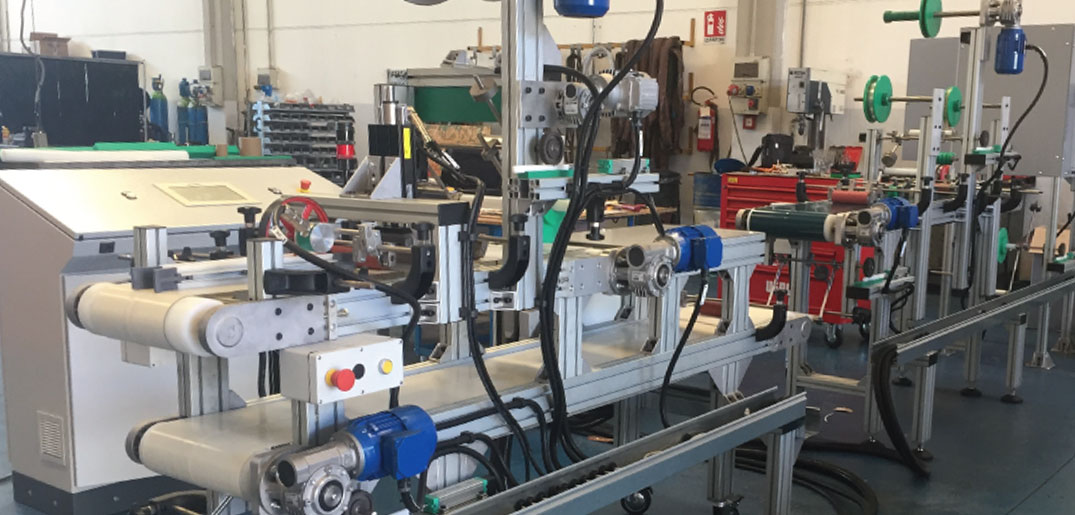
Built with the use of new materials, with innovative mechanical solutions and customized management software.
Telescopic excursion that allows the transport of the material at greater distances with little encumbrances without inhibiting the normal work areas.
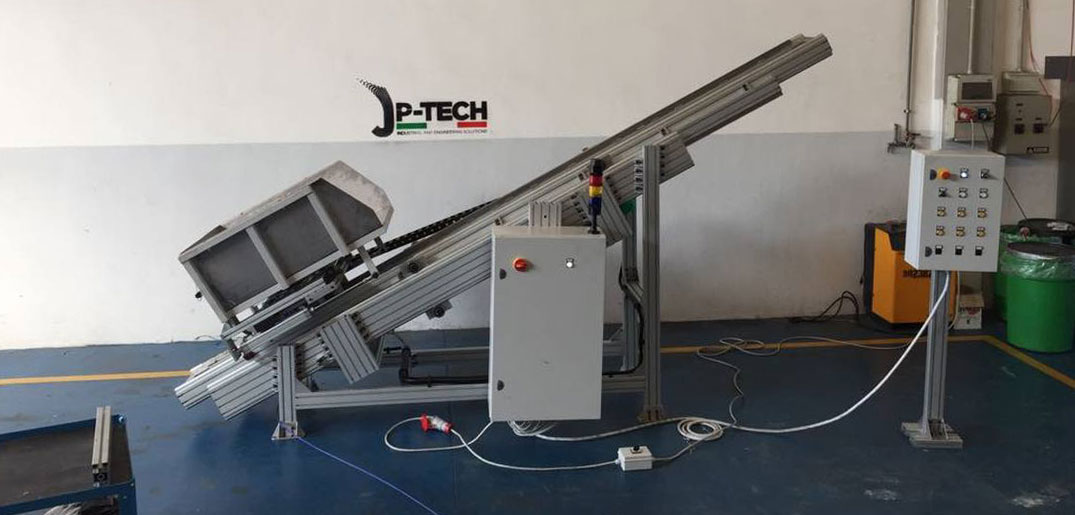
This machine was created to solve the need of one of our customers in the silicone sector who has patented and designed this new product.
The combination of our experience on talcers for silicone combined with the study and management of towing, has given life to a light and compact solution, able to be moved on different production lines and able to TALC and WIND A SILICONE CORD IN COILS RAW.
The specific need was to pack the product described above in reels respecting weights and diameters. A small car but a big challenge.
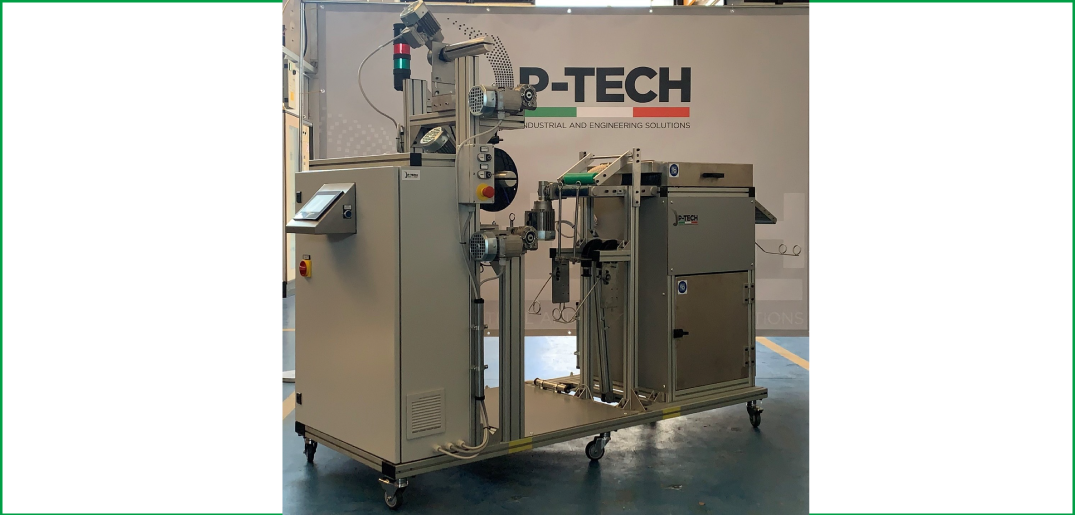
JP-SM2
This machine represents our solution to cut square or round silicone LOGs according to the need.
Our LOG SIZE can be positioned for example at the exit of Extruders, Mixers with double Z reels with unloading screw and Filter Presses.
The cutting length is carried out with the positioning of the appropriate photoelectric barrier sensor at height; the piston cuts and then the tape accelerates speed to facilitate the detachment of the cut LOG.
The machine can also, if required, be included in the industry 4.0 plan by optioning it with a touch screen control panel, software for collecting and sending production data to the management system, remote management system and recipe book.
This is just one of the machines that JP-TECH builds for raw silicone packaging
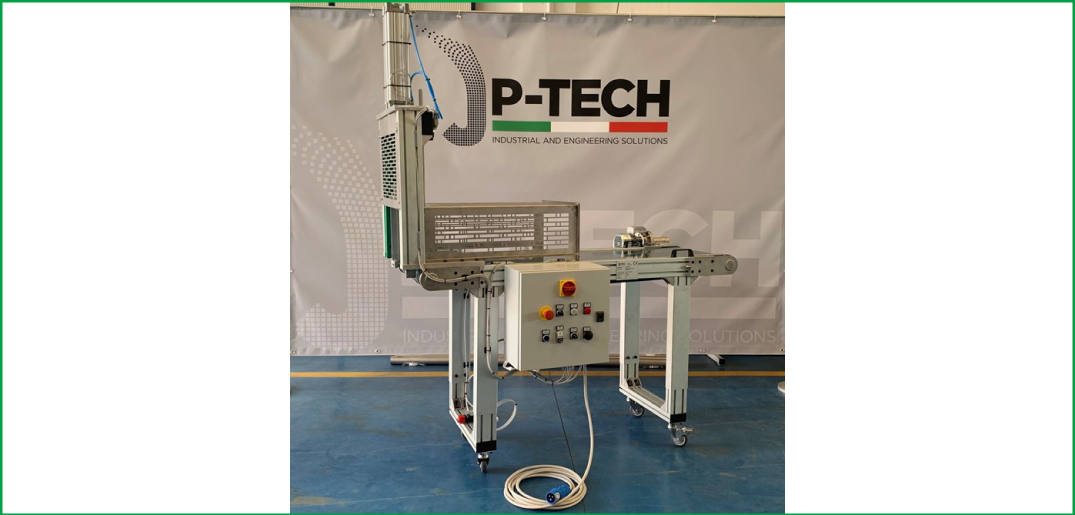
Also this machine designed and built by us has aroused considerable interest in all cases where it is necessary to pack talc and rolled strips (pizzas).
The two models differ only in the capacity of make pizzas with a maximum diameter of 500 and 800 mm respectively.
The maximum working speed is 20 meters per minute.
The manual or automatic speed adjustment option is also available on this machine.
All parameters and functions are programmable from the keyboard; the use of the machine is simple and immediate.
The operator sets the desired strip cutting length and then inserts the end of the strip into the special locking system, starts the first plate and starts wrapping: once the set length is reached, the machine performs the cut and the 1st plate ends the 'wrapping; the operator repeats the wrapping start-up operation on the 2nd plate and, while this is working, frees the 1st plate from the product.
By alternating the two plates, the wrapping cycle is continuous, therefore it is never necessary to stop the machine.
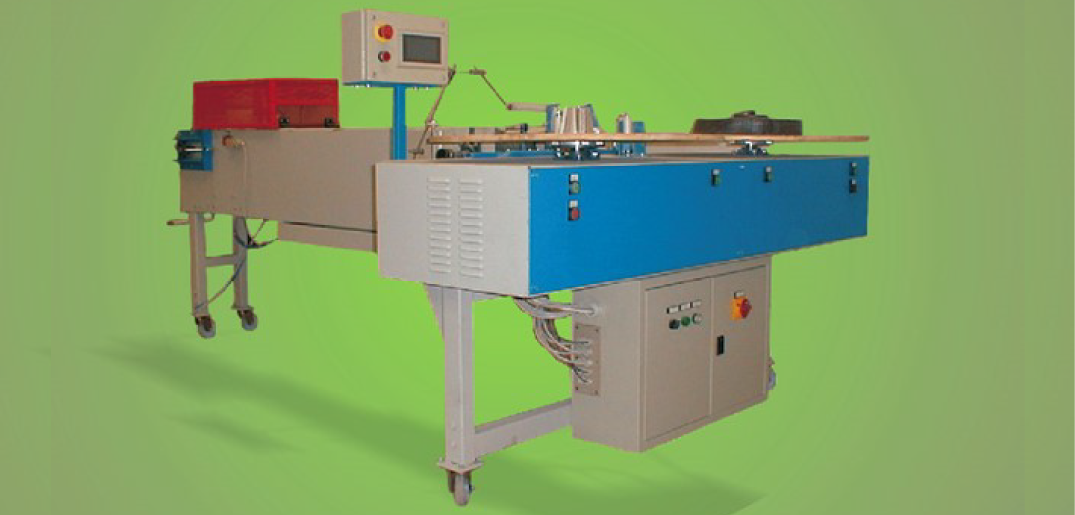
The Polythene 400 machine is used when the strip cannot be powdered to avoid pollution.
It too can be used by manually and / or automatically adjusting the speed (from 0 to 15 meters per minute).
The start-up operation is extremely simple, and the packaging of the strip wrapped in polythene is always effective.
The machine is mounted on wheels: it can therefore be used in combination with different strip supply lines.
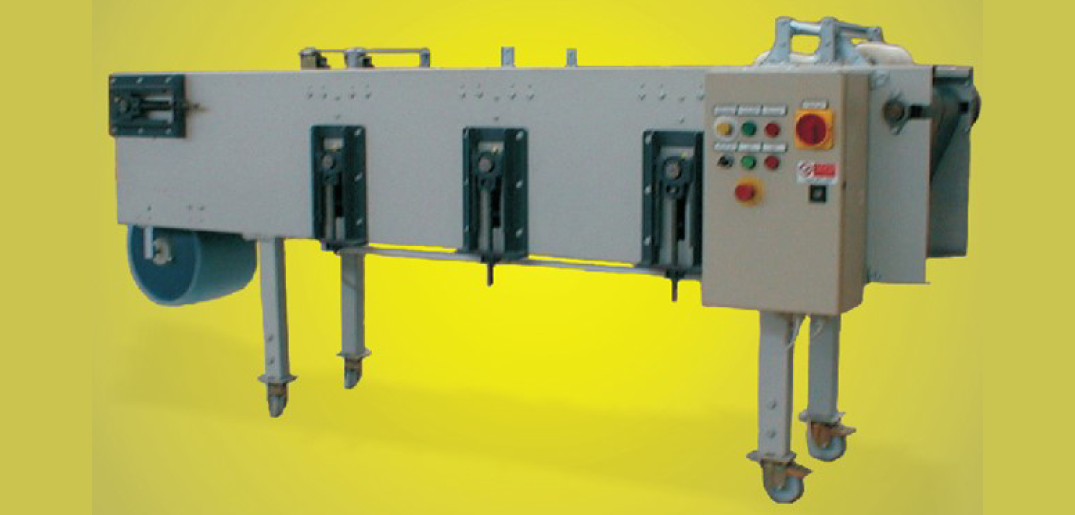