La JP-TECH negli anni ha sviluppato al suo interno un protocollo che le consente di ottenere ottimi risultati per quanto riguarda la progettazione e costruzione dei suoi macchinari oltre che alla fase di collaudo e messa in funzione.
- Tutto parte dalla fase di studio e analisi delle problematiche da risolvere
- Successivamente si passa alla fase progettuale in cui la JP-TECH si interfaccia con i suoi tecnici e con i suoi collaboratori per la messa a punto del progetto.
- Ora è il momento della costruzione, JP-TECH nella sua sede produttiva costruisce internamente la gran parte dei componenti e si occupa dell’assemblaggio dell’intera macchina/linea.
- Dopo la realizzazione del macchinario/linea, JP-TECH nella propria sede effettua il collaudo con il materiale di riferimento (fornito dal cliente).
- Una volta eseguiti scrupolosi test di verifica e collaudo, JP-TECH si occupa anche dell’installazione presso il cliente.
- Infine viene eseguito un ulteriore collaudo presso il cliente e in contemporanea vengono consegnate tutte le documentazioni necessarie all’azienda per definire il macchinario come “PRONTO E UTILIZZABILE”.
PROGETTO
JP-LCS 028
La Calandra di nuova costruzione, è nello specifico una calandra a 3 cilindri con configurazione a “Y”, opzionata per garantire velocità e frizione variabile, il tutto per garantire al cliente di poter lavorare diversi prodotti.
Oltre al macchinario primario abbiamo fornito anche le macchine accessorie, a completamento di una linea che può lavorare tutti i prodotti dell’azienda cliente.
In particolare la linea è dotata di:
- Sistema di telatura con cambio bobina “in corsa”
- Macchina per taglio, recupero sfridi e Goffratura del materiale
- Macchina per il riscaldamento del prodotto e se necessario applicazione di materiale speciale
- Macchina per il raffreddamento del prodotto
- Avvolgitore automatico
La linea è completamente accessoriata per il controllo e la lettura dei dati come da Piano Industria 4.0.
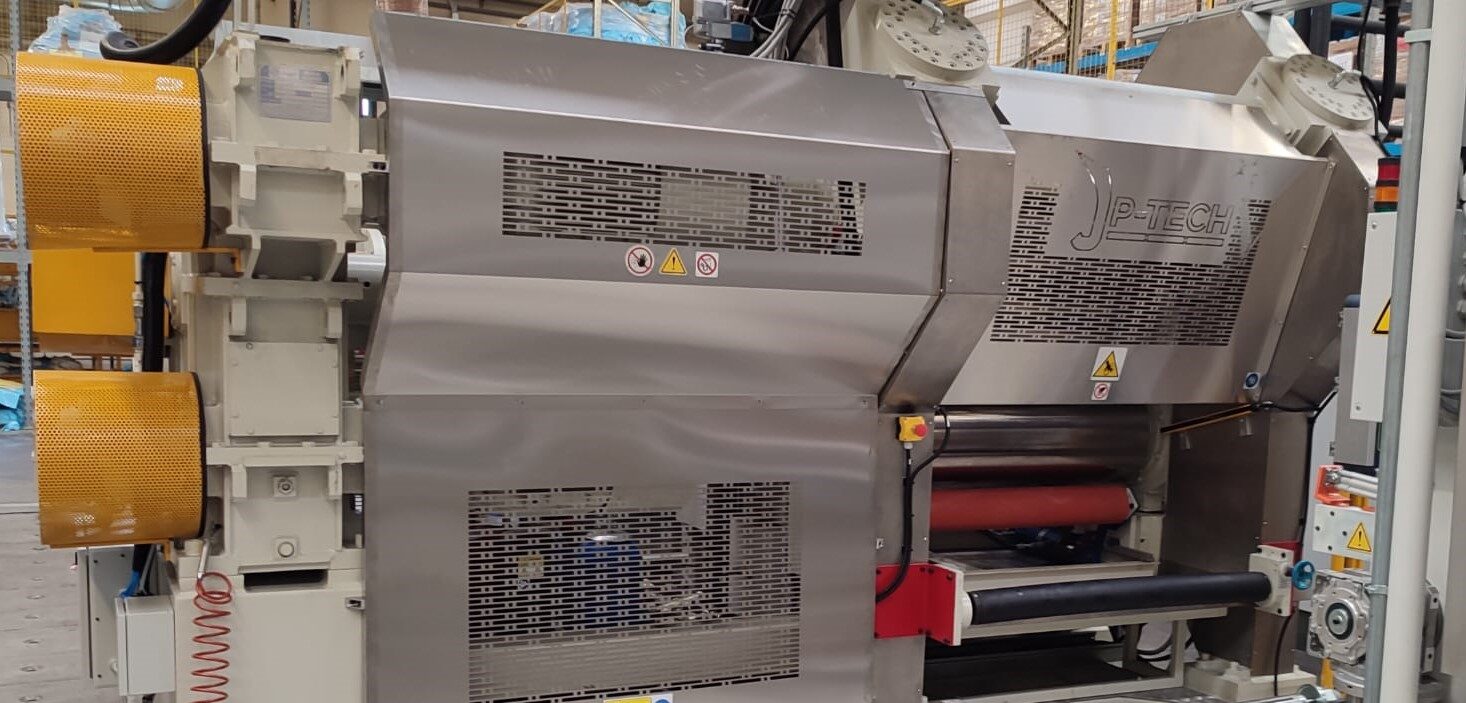
La macchina è stata completamente revisionata a nuovo, anzi abbiamo fatto molto di più.
Sulla macchina sono stati installati per la prima volta al mondo i sistemi Elettroidrostatici di MOOG che consentiranno alla macchina lo spostamento del cilindro mobile con pochi litri di olio (i sistemi precedenti ne utilizzavano circa 200), oltre che consumi di energia pressoché inesistenti.
JP-TECH è da anni che propone sul mercato macchine green con applicate le ultime tecnologie per il settore. L’attenzione ai consumi di energia e olio è da sempre un punto di forza di JP-TECH.
Un sentito ringraziamento va al nostro cliente Vibram Group per aver accettato la sfida di montare questi innovativi sistemi. Vibram da anni punta alla sostenibilità ed a un Totally Green della produzione, grazie ad uno staff attento alle esigenze tecnologiche di mercato e sempre pronto ad adottare le soluzione più innovative.
Un grazie speciale va ai nostri Partner che hanno collaborato con noi per raggiungere questo obiettivo Moog Inc. ROGAL S.R.L. Multi Data s.r.l. Maier Italia @UTP TP Tecnologie Pneumatiche Sella Srl
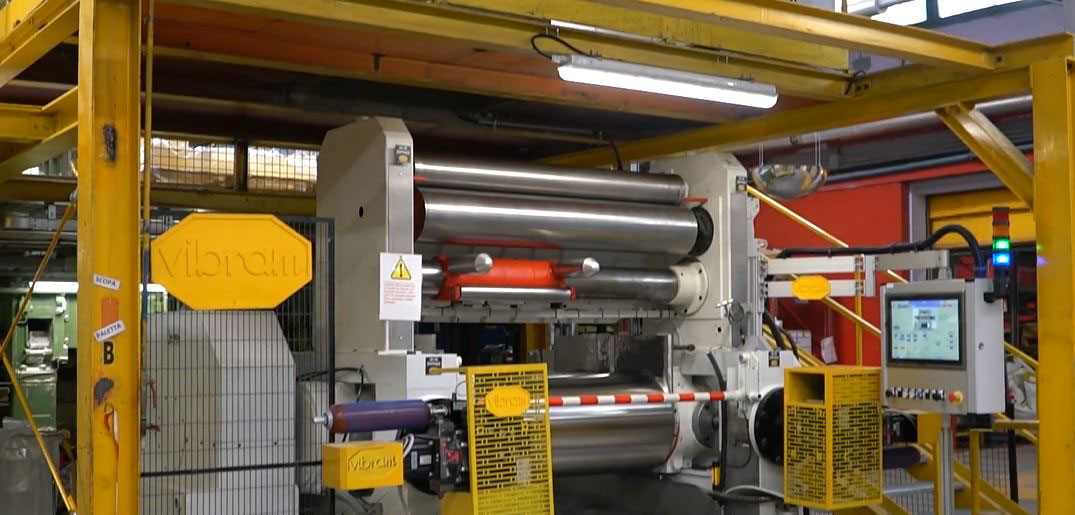
JP-MJR3
Il mescolatore a cilindri per gomma JP-MJR3 è una macchina che oltre a rispettare tutte le particolarità e le caratteristiche dei precedenti modelli nati in JP-TECH, “è stata arricchita con delle” novità.
Montati su di essa ci sono i nuovi sistemi EAS nati in collaborazione con Moog che ora sono stati migliorati con la parte da noi brevettata che li rende ancora più efficienti e sostenibili.
Oltre ai nuovi sistemi brevettati abbiamo implementato il nostro Software con la gestione automatica di tutte le fasi di mescolazione.
Il software è stato migliorato anche nel controllo del risparmio energetico e nel controllo della componentistica presente sulla macchina.
Il software è in grado di avvisare l’operatore e i tecnici della manutenzione di eseguire i controlli dei liquidi di lubrificazione, ingrassaggio delle guide e controllo dell’usura del sistema frenante, oltre a molte altre segnalazioni.
Altra parte fondamentale è il controllo costante dei sistemi di sicurezza.
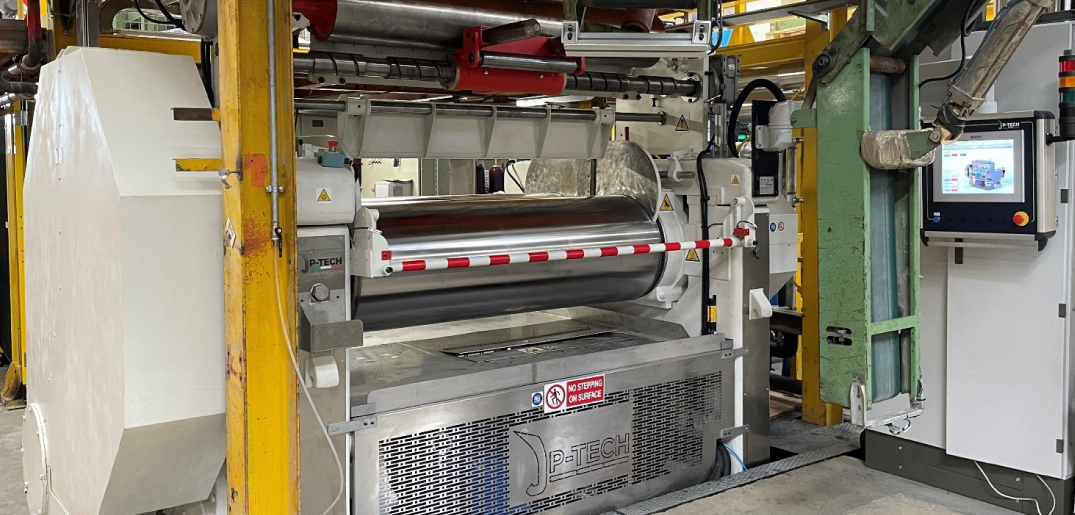
ELSA JP-AG002 DG
Dimensioni compatte e con possibilità di disporre l’impianto con lay-out variabili.
La linea è composta da diversi blocchi primari che sono in realtà quattro diverse macchine utilizzabili anche come macchine autonome.
Il magazzino automatico del prodotto da lavorare è termostatato e può mantenere il prodotto a temperatura sia in riscaldamento che in raffreddamento.
La pressa filtro, che può funzionare automaticamente, fornendo informazioni precise sullo stato del processo di produzione del prodotto.
Trommel completo di unità di taglio e incorniciatura con sistema integrato, raffreddamento del prodotto finito.
Il sistema consente di lavorare in: manuale, semi automatico, automatico con pannello operatore, modulo vocale e sistema di acquisizione dati. Una serie di dati e informazioni è disponibile sia per l'operatore che per il laboratorio di controllo qualità.
La linea ELSA è un insieme di decenni di esperienza lavorativa e costruzione di prodotti con tecnologia avanzata che ne fanno una novità assoluta nella lavorazione di Gomma, Silicone, Viton e altri prodotti.
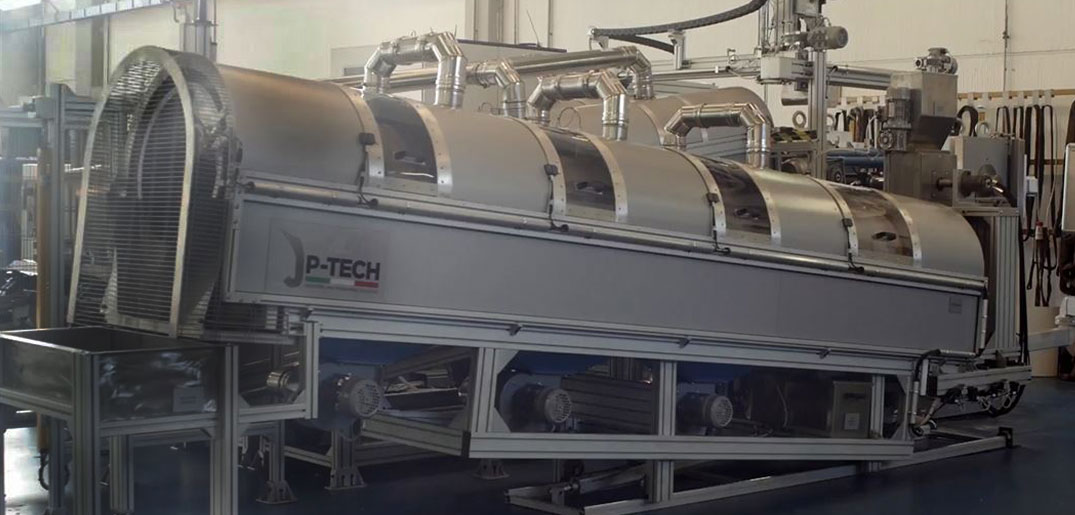
Lisa è in grado di gestire tutte le operazioni da eseguire completamente in automatico.
I parametri vengono inseriti tramite un touch-screen su cui vengono visualizzate tutte le parti che compongono la macchina con i relativi dati.
Le fasi di lavoro gestite da LISA sono:
1- Svolgitura della bobina del profilo in Gomma
2- Accoppiamento con il biadesivo
3- Distaccamento della protezione del biadesivo
4- Recupero della pellicola protettiva del biadesivo
5- Applicazione della protezione in polietilene
6- Avvolgitura-taglio netto-mezzo taglio.
7- Gestione automatica della velocità dei nastri per mantenere la giusta trazione della gomma e sincronizzazione delle velocità delle bobine durante le fasi di accoppiamento, taglio e avvolgitura.
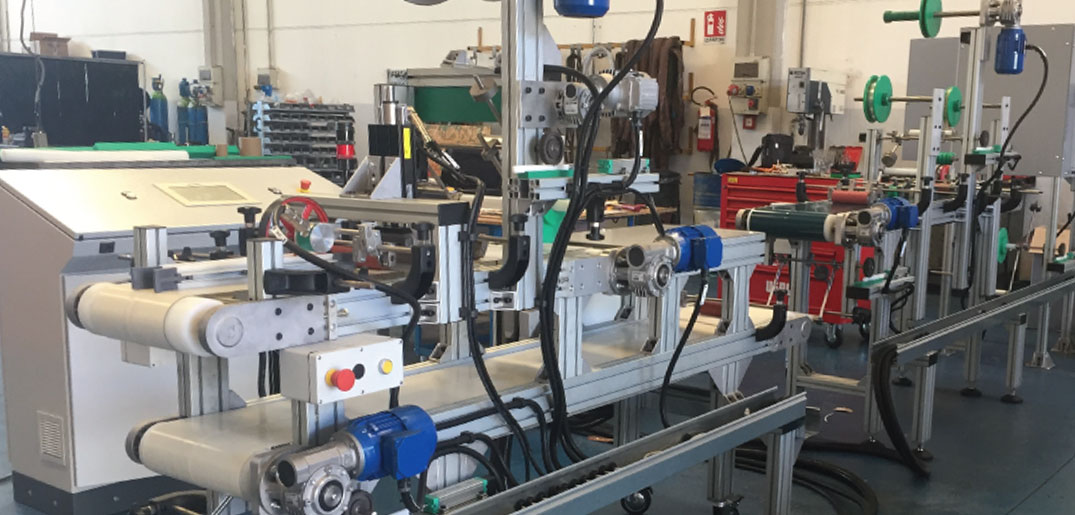
Costruito con utilizzo di nuovi materiali, con innovative soluzioni meccaniche e software di gestione personalizzato.
Escursione telescopica che consente con piccoli ingombri il trasporto del materiale a distanze maggiori senza inibire le normali zone di lavoro.
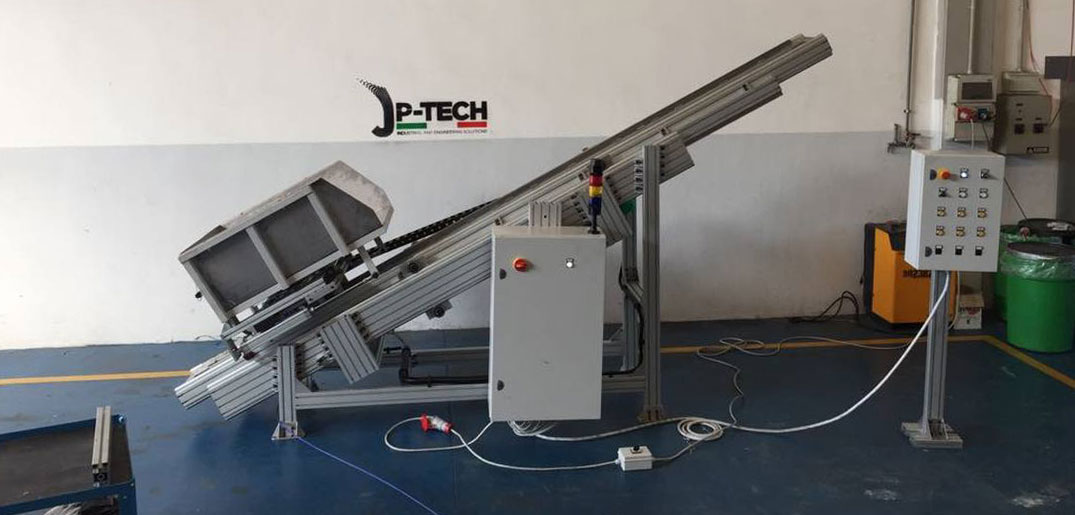
Questa macchina nasce per risolvere l’esigenza di un nostro cliente nel settore silicone che ha brevettato e ideato questo nuovo prodotto.
L’unione della nostra esperienza sui talcatori per silicone unita allo studio e gestione dei traini, ha dato vita ad una soluzione leggera e compatta, in grado di essere spostata su diverse linee produttive e in grado di TALCARE e AVVOLGERE IN BOBINE UN CORDINO DI SILICONE CRUDO.
L’esigenza specifica era quella di confezionare in bobina il prodotto sopra descritto rispettando pesi e diametri. Una piccola macchina ma una grande sfida.
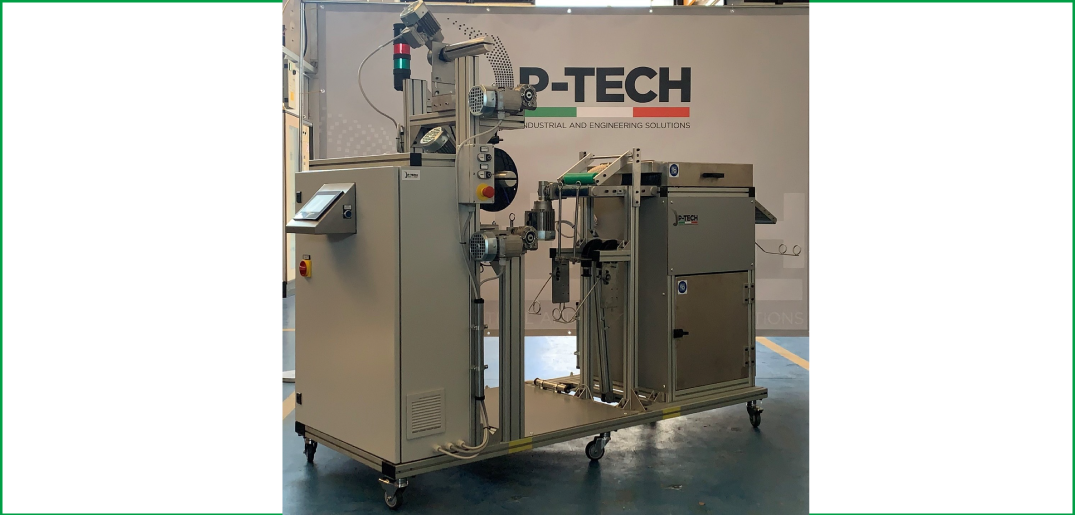
JP-SM2
NUOVO TAGLIA LOG 2021/200.
Questa macchina rappresenta la nostra soluzione per tagliare LOG di silicone quadri o tondi a seconda dell'esigenza.
Il nostro TAGLIA LOG è posizionabile per esempio all'uscita di Estrusori, Mescolatori con aspi a doppia Z con coclea di scarico e Presse Filtro.
La lunghezza di taglio è effettuata con il posizionamento in quota dell’apposito sensore fotoelettrico a sbarramento; il pistone effettua il taglio e successivamente il nastro ha un’accelerazione di velocità per facilitare il distaccamento del LOG tagliato.
La macchina può inoltre se richiesto rientrare nel piano industria 4.0 opzionandola con pannello di controllo Touch screen, software per raccolta e invio su gestionale dei dati di produzione, sistema di gestione da remoto e ricettario.
Questa è solo una delle macchine che JP-TECH costruisce per il confezionamento del silicone a crudo.
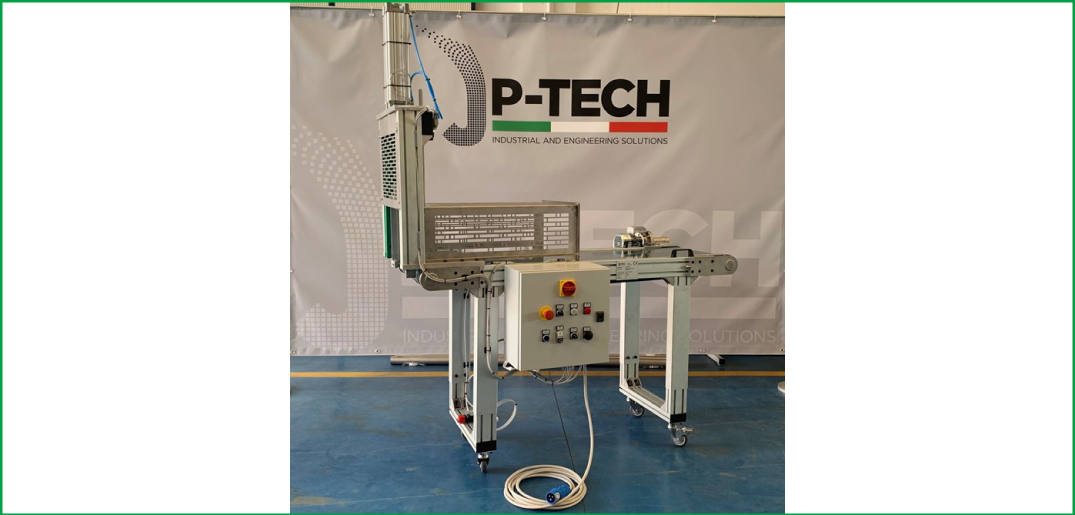
Anche questa macchina da noi progettata e realizzata ha riscosso notevole interesse in tutti i casi ove si rende necessario il confezionamento di strisce talcate ed arrotolate (pizze).
I due modelli si differenziano esclusivamente per la capacità di
realizzare pizze che hanno come diametro massimo rispettivamente 500 e 800 mm.
La velocità massima di lavoro è pari a 20 metri al minuto.
Anche su questa macchina è prevista l’opzione di regolazione velocità manuale o automatica.
Tutti i parametri e le funzioni sono programmabili da tastiera; l’utilizzo della macchina risulta semplice ed immediato.
L’operatore imposta la lunghezza di taglio striscia desiderata e quindi inserisce il capo della striscia nell’apposito sistema di blocco, avvia il primo piatto ed inizia l’avvolgitura: raggiunta la lunghezza impostata la macchina effettua il taglio ed il 1° piatto termina l’avvolgitura; l’operatore ripete l’operazione di avviamento avvolgitura sul 2° piatto e, mentre questo lavora, libera il 1° piatto dal prodotto.
Alternando i due piatti il ciclo di avvolgitura risulta continuo, pertanto non è mai necessario fermare la macchina.
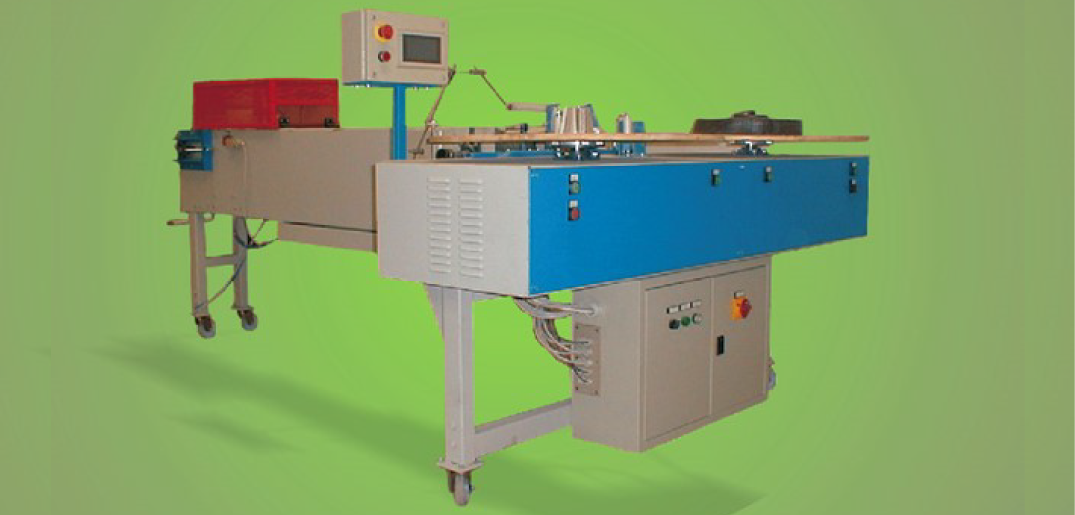
La macchina Politene 400 viene impiegata quando la striscia, per evitare inquinamenti, non può essere talcata.
Anch’essa può essere utilizzata regolando manualmente e/o in automatico la velocità (da 0 a 15 metri al minuto).
L’operazione di avviamento risulta estremamente semplice, ed il confezionamento della striscia avvolta in politene sempre efficace.
La macchina è montata su ruote: permette quindi di essere utilizzata in abbinamento a diverse linee fornitrici di striscia.
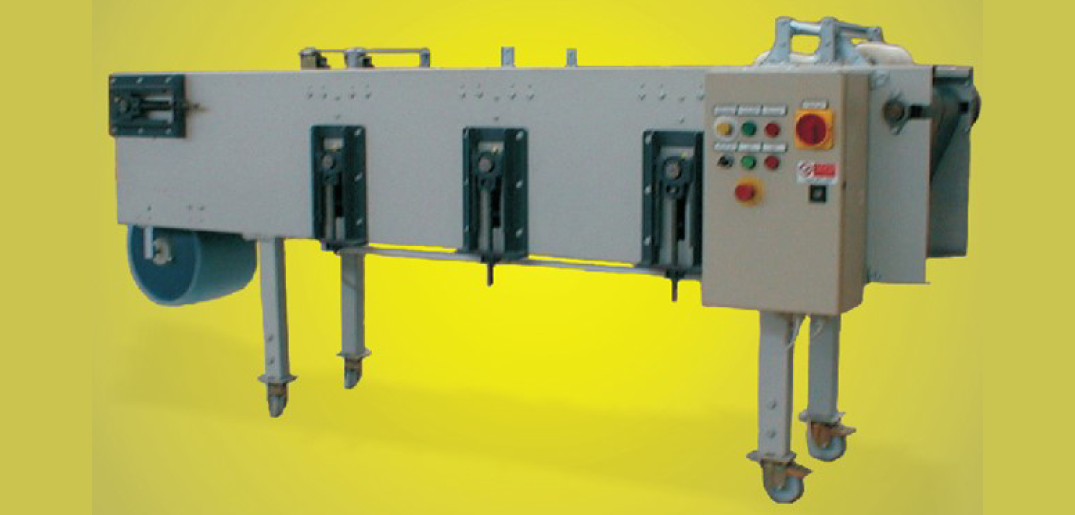